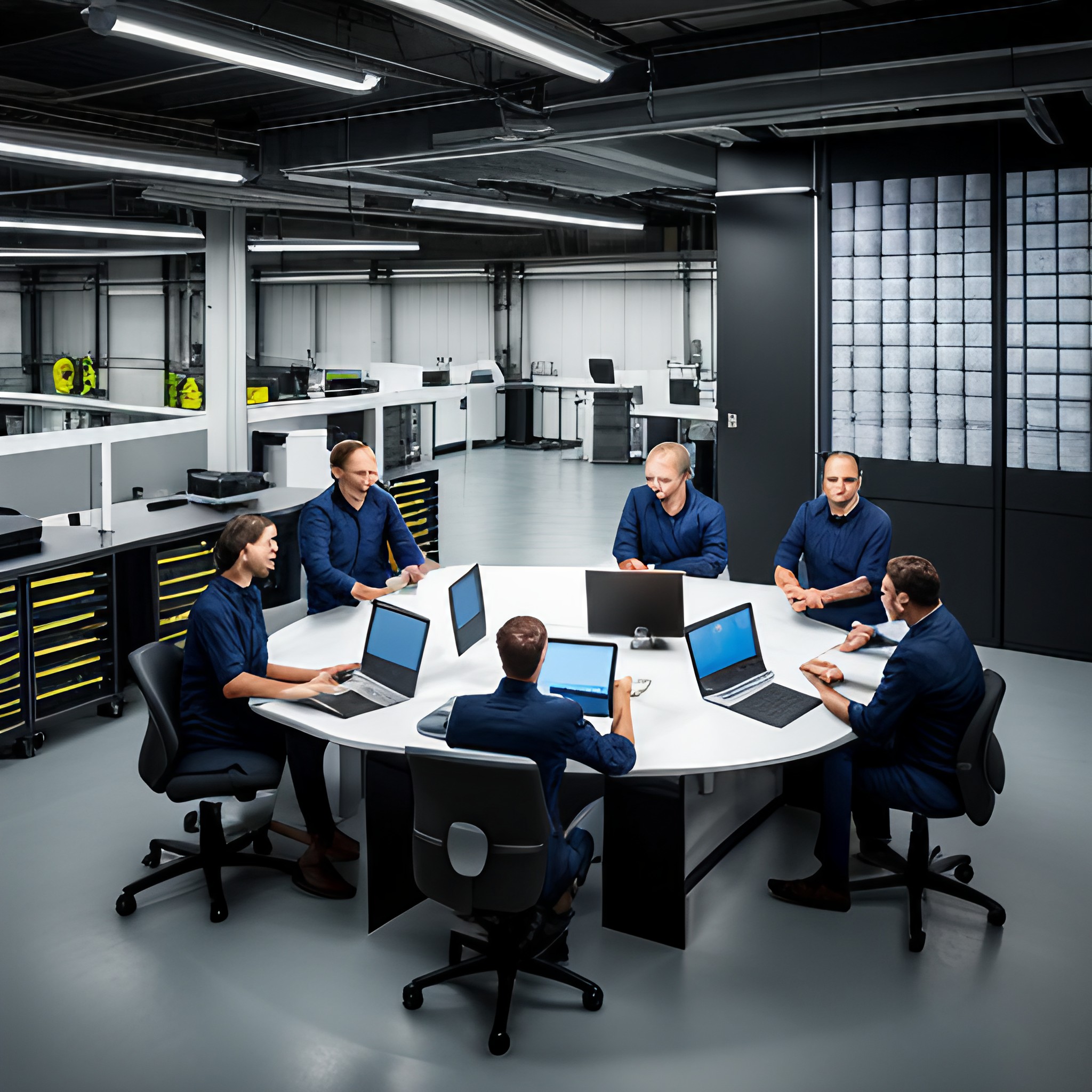
Unlocking Quality Control with Digital Innovation
In an era awash with technological promise, the manufacturing industry finds itself at a crossroads. Traditional quality control paradigms, long the bedrock of product integrity, are proving increasingly inadequate in grappling with the complex demands of modern production. Digital transformation stands not as a mere convenience but as an imperative for businesses seeking to maintain competitive edges and consumer trust.
Executive Summary
The nexus of quality control and digital innovation heralds a pivotal transformation in the manufacturing landscape, offering a multifaceted strategy to meet and exceed the evolving quality requirements of today's production demands. Traditionally, quality assurance and quality management have been dependent on manual inspections and the tacit knowledge of quality control professionals. However, the complexity and scale of modern manufacturing necessitate a more integrated approach, blending rigorous quality control methods with the agility afforded by digital transformation initiatives.
Digital transformation strategy emerges as a cardinal pillar for businesses, enabling an unparalleled alignment of quality control activities with overall business strategy. This integration extends across the supply chain, enhancing the capability of businesses to operate efficiently and to ensure the quality of final products meets customer expectations. Through the adoption of digital technologies—ranging from statistical process control to artificial intelligence—quality control processes become more predictive, adaptive, and responsive to manufacturing variances, fundamentally changing the way quality assurance is conceived and implemented.
Furthermore, digital transformation efforts facilitate a seamless collaboration between quality control inspectors and other professionals within the organization, including quality engineers, software developers, and project managers. This collaborative environment fosters innovation, expediting the development of new business models that are responsive to customer demands and resilient to changes in the market.
In the face of these advancements, government agencies, quality specialist professionals, and chief executive officers must recognize the importance of investing in digital technologies, not only as a means to enhance product quality but also to foster a culture of continuous improvement and innovation within their organizations. By harnessing data analytics and advanced software testing methods, businesses can ensure that their products are reliable, meet specified requirements, and enhance the customer experience.
The shift towards digital transformation requires organizations to rethink their approach to quality control, moving beyond legacy technologies and traditional business models. It demands a strategic vision that places quality management at the heart of business processes, leveraging digital innovation to drive process improvement and fulfill customer requirements effectively. In doing so, organizations can achieve competitive advantage, ensuring that their products are not only free from defects but also align with the shifting paradigms of global manufacturing and public health standards.
Understanding Quality Control and Quality Assurance
Quality control (QC) and quality assurance (QA) are two pivotal components of quality management, ensuring that products not only meet customer and regulatory requirements but excel in terms of integrity and reliability. This section delineates the fundamental aspects of these concepts and their role in the contemporary manufacturing landscape, incorporating the implications of digital transformation.
The Essence of Quality Control
Quality control pertains to the operational techniques and activities used to fulfill quality requirements for a product. At its core, QC involves a series of inspections, tests, and measurements to ensure that the product quality is maintained or improved. Quality control professionals, including quality engineers and inspectors, deploy various quality control methods, ranging from statistical process control to meticulous examinations of final products. These methods help in identifying and rectifying defects or deviations in the manufacturing processes, thereby preventing defective products from reaching the customer.
The Role of Quality Assurance
Quality assurance, by contrast, is a broader concept encompassing all planned and systematic activities implemented within the quality system to provide confidence that a product or service will fulfill requirements for quality. QA activities involve the entire manufacturing processes and business processes, focusing on preventing defects through planned and systematic actions. This includes everything from verifying the quality of raw materials, through software testing in software development, to ensuring the efficacy of the final product in fulfilling specified requirements.
Digital Transformation and Quality Management
In an age where digital technologies are fundamentally altering business models and processes, the integration of digital transformation initiatives into quality management has become paramount. This transition not just involves the adoption of new technologies like artificial intelligence and data analytics but also requires a profound cultural shift within organizations. The aim is to leverage digital transformation efforts to enhance the effectiveness of quality control processes and QA strategies, enabling innovation and ensuring product integrity in a highly competitive market.
Harnessing Digital Technology for QC and QA
Digital transformation strategy for QC and QA involves employing advanced digital technologies to streamline and improve the reliability of quality control activities and assurance processes. This includes employing statistical process control software empowered with artificial intelligence to predict and prevent defects in manufacturing processes more accurately. Digital transformation initiatives also facilitate better data analysis, allowing businesses to operate more efficiently and respond more swiftly to customer demands and changes in public health standards or regulatory environments.
Business leaders, including CEOs and C-suite officers, play a crucial role in advocating for and directing investments in digital transformation efforts. Their leadership is critical in ensuring that digital transformation projects align with overall business strategy and supply chain management objectives, driving process improvement, and fostering new business models that prioritize quality and customer experience.
Quality control and quality assurance are indispensable elements of quality management, crucial for ensuring that products meet or exceed the rigorous standards of today's markets. The incorporation of digital transformation initiatives into QC and QA is not optional but a necessity for businesses aiming to maintain relevance and competitiveness. Through strategic investment in digital technologies and a commitment to fostering a culture of continuous improvement, organizations can achieve higher levels of product quality and reliability, ultimately enhancing customer satisfaction and trust.
The Shortcomings of Tradition in the Modern Market
Once, quality control was a term easily defined, its practice synonymous with precision and defect eradication. However, the intricacies of modern supply chains, coupled with the accelerated pace of production, have rendered traditional quality control methods insufficient. Legacy inspection processes are too often retrospective, catching defects after the fact and at great expense, both in time and resources.
The speed and scale of today's manufacturing require a paradigm shift. Spot inspection and manual sampling methods, while venerable, can bottleneck agility and lead times. They also face challenges in consistency and human error. In essence, the traditional approach is a constraint in the race for quality against the clock and the markets.
Prioritizing Progress Through Digital Transformation
Enter digital transformation — the strategic integration of digital technology into all areas of a business, fundamentally changing how you operate and deliver value to customers. This sweeping change opens doors to continuous monitoring, real-time feedback loops, and data-driven decision making. Quality control, reimagined in a digital context, becomes proactive rather than merely reactive, with the ability to detect, address, and prevent issues well before products reach end-users.
To illustrate, consider the surge in smart factories, where interconnected systems leverage Internet of Things (IoT) technologies to self-regulate, adapt, and optimize processes. These digital ecosystems foster a culture of constant refinement, where fluctuations or anomalies in production are instantly flagged, investigated, and remedied. This is a safeguard not only for immediate product integrity but also for the consistency of the brand's promise and reputation.
Implementing a Digital QA and QC Framework in Your Organization
Implementing a digital Quality Assurance (QA) and Quality Control (QC) practice within an organization requires a strategic, comprehensive approach to integrate new technologies and methodologies with existing business processes. This transition towards a digital QA/QC framework involves several critical steps, tailored to meet quality requirements and leverage digital transformation efforts for optimal efficiency and product quality.
Step 1: Developing a Digital Transformation Strategy
The first step involves the development of a digital transformation strategy that aligns with the company's overall business strategy, particularly focusing on quality management and supply chain management. CEOs, C-suite officers, and business leaders must champion these digital transformation initiatives, prioritizing investments in digital technologies that foster process improvement and support new business models. This strategy should clearly articulate the role of digital transformation in enhancing quality control processes and QA practices, from software development to food production lines.
Step 2: Identifying and Implementing Digital Technologies
The adoption of digital technologies is central to transforming quality control and assurance practices. Organizations should invest in statistical process control software, data analytics, and artificial intelligence to enhance the precision of quality control methods and facilitate real-time data analysis. These technologies can improve the reliability of quality control activities, enabling quality control professionals and inspectors to predict and prevent defects more accurately. Implementing such technologies requires a thorough evaluation of legacy technologies and processes, with a focus on integrating new solutions that streamline manufacturing processes and business process management.
Step 3: Training and Development for Digital QC and QA
Transitioning to a digital QA and QC framework necessitates significant training and development efforts to equip quality control specialists, engineers, and inspectors with the necessary skills. Organizations should focus on developing expertise in digital transformation initiatives, project management, data analytics, and the use of AI in quality control. This involves not only technical training but also fostering an organizational culture that embraces continuous learning and adaptation.
Step 4: Collaborating with Government Agencies and International Organizations
To ensure that digital QA and QC practices meet customers' specified requirements and adhere to regulatory standards, businesses should actively collaborate with government agencies, international organizations, and industry associations. This collaboration can help organizations stay abreast of changes in public health standards, supply chain regulations, and quality assurance best practices. It also facilitates a more standardized approach to fulfilling quality requirements across various industries.
Step 5: Adjusting Business Processes and Quality Management Systems
Incorporating digital transformation efforts into QA and QC requires meticulous adjustments to business processes and quality management systems. Organizations need to redefine job titles, roles, and responsibilities to reflect the distinct differences introduced by digital technologies. This may involve creating new career paths for quality control inspectors, quality specialists, and quality engineers, ensuring they can effectively leverage digital tools to monitor and ensure product quality.
Step 6: Continuous Evaluation and Improvement
Finally, implementing a digital QA and QC practice is an ongoing process that demands continuous evaluation and improvement. Organizations should employ a robust project management framework to monitor the effectiveness of digital transformation efforts, identifying opportunities for process improvement and innovation. Regular feedback loops, involving all stakeholders from the production line to the C-suite, are essential to ensure that the organization's digital QA and QC practices evolve to meet changing customer demands and market conditions.
Through strategic investment in digital technologies, comprehensive training and development, and a commitment to continuous improvement, organizations can fundamentally transform their QA and QC practices. This not only enhances the quality of products and services but also positions companies to thrive in a competitive, rapidly changing marketplace.
Challenges in Digitally Transforming QA and QC Processes
While the digital transformation of Quality Assurance (QA) and Quality Control (QC) presents unprecedented opportunities for efficiency and product quality enhancement, organizations face several significant challenges throughout this transition.
Cultural and Organizational Resistance
One of the foremost barriers is the cultural and organizational resistance to change. Shifting from traditional methodologies to a digital-first approach requires not only technological upgrades but also a fundamental change in mindset and operations. Employees may exhibit skepticism towards new technologies or methods, fearing job displacement or doubting the effectiveness of new systems. Overcoming this resistance necessitates proactive leadership, comprehensive training, and clear communication about the benefits and necessity of digital transformation.
Integration of Digital Technologies with Existing Systems
Integrating advanced digital technologies, such as AI and data analytics, with legacy systems can be technically challenging and resource-intensive. Compatibility issues may arise, necessitating significant modifications to existing infrastructures or even complete overhauls. This process requires meticulous planning, significant investment, and often a phased implementation approach to ensure continuity of operations.
Data Security and Privacy Concerns
The increased reliance on digital technologies for QA and QC introduces heightened data security and privacy concerns. Organizations must safeguard sensitive data against breaches, which can compromise customer trust and result in regulatory non-compliance. Implementing robust cybersecurity measures and ensuring compliance with international data protection regulations are imperative, yet complex, tasks.
Skill Gaps and Workforce Transformation
The digital transformation of QA and QC processes requires a workforce with expertise in data analytics, machine learning, and digital project management, among other areas. However, the existing skill gaps in the workforce can hinder this transition. Organizations must invest in comprehensive training and possibly recruit new talent with the requisite digital skills, which can be a time-consuming and expensive endeavor.
Continuous Adaptation to Technological Advancements
Technology evolves at a rapid pace, and keeping up with the latest advancements is critical to maintaining a competitive edge. Organizations must foster a culture of continuous learning and innovation, which can be challenging in a fast-moving digital landscape. This necessitates ongoing investment in technology and training, as well as a strategic approach to innovation management.
Regulatory Compliance and Standardization
As digital technologies become more integral to QA and QC processes, organizations must ensure compliance with an increasingly complex landscape of international standards and regulations. Adapting to these changing regulatory requirements can be challenging, especially for global organizations that operate across multiple jurisdictions with varying standards.
Addressing these challenges requires a holistic approach, combining strategic planning, investment in technology and human capital, and a commitment to cultural change. By navigating these obstacles effectively, organizations can unlock the full potential of digital transformation in their QA and QC processes, thereby enhancing product quality and operational efficiency.
Real-World Success Stories of Digital Quality
The success stories are not relegated to the theoretical. Leading corporations are leveraging digital transformation with astonishing results. Tesla, in its visionary intertwining of AI with its manufacturing fabric, promulgates a model of excellence through predictive maintenance in real time. This digital fortitude has drastically reduced downtime and improved product quality, setting unprecedented benchmarks in an industry notorious for its challenges.
IBM's Watson for quality control in manufacturing is another beacon, illuminating the potential of cognitive computing. By employing AI and IoT, Watson can process and analyze vast datasets in seconds, identifying defects that elude human senses and traditional oversight mechanisms. This speed and acuity in defect detection result in savings and efficiencies that are a testament to the power of digital integration.
Alibaba, too, in its judicious use of analytics and AI in warehousing, showcases how harmonizing various digital tools can enhance operational excellence. By enabling smart logistics with cutting-edge technologies, the e-commerce giant has honed its ability to serve customers with a level of precision and speed that was unimaginable a mere decade ago.
AI and Data Analytics at the Helm of a New Era
The heart of digital transformation in quality control throbs with the cadence of artificial intelligence and data analytics. AI's machine learning algorithms lay bare new avenues of efficient defect prediction and root cause analysis, while data analytics not only enhances existing data but also enables the discovery of novel parameters and indicators of quality. Production that learns, adjusts, and evolves in real time is no longer the exclusive purview of science fiction — it is an operational benchmark waiting to be achieved.
Predictive maintenance, for instance, has found an adept practitioner in the form of AI. By analyzing sensor data and equipment performance against historical trends, AI can forecast when maintenance is needed, thus preventing unexpected downtimes and maintaining equipment at peak efficiency. The implications for product quality assurance and control are manifold, as uninterrupted operations carry the dual benefits of consistent production and reduced waste.
A Glimpse into the Future of Quality Control
The trajectory of quality control is not one fixed in stasis, but one arc-bound toward innovation and adaptability. Digital twins, or virtual representations of physical objects or systems across their lifecycles, offer us a profound future insight into quality control. By simulating and analyzing these twins, manufacturers can optimize real-world production processes, predict failures, and even imagine and test remedies or future iterations.
The evolution driven by digital innovation does not speak to mere efficiency and the bottom line. It resonates at the very core of a brand's bond with its customers. In a digitally empowered age, product quality is an all-encompassing experience — from design to delivery, and beyond. The companies that appreciate this signaling moment in industry evolution stand poised to redefine quality not merely as an end product but as an ethos threaded through their very business fabric.
Steering Your Enterprise Toward Digital Quality Prowess
It is not a question of if but when your enterprise will realize the digital destiny of its quality control efforts. The path forward necessitates shrewd investment, comprehensive training, and an organizational culture that values and champions digital aptitude. Leaders in this space will not only enjoy operational efficiencies and market advantages but will also be architects of a new narrative — one where quality control and digital integration become synonymous with an enterprise's legacy.
The symbiosis between technology and quality control is undeniable, and its potential is boundless. This is the clarion call for the manufacturing industry at large. Together, as we forge ahead into an increasingly digital world, we lay the bricks for a future where quality is a result not of happenstance but of strategic, digital alchemy.
In the rapidly evolving landscape of manufacturing and business, the interplay between digital transformation and quality control marks the dawn of a new era in operational excellence. Quality control (QC) and quality assurance (QA) have traditionally been the linchpins ensuring that products meet specified requirements, with quality management (QM) systems orchestrating these activities to fulfill quality requirements comprehensively. However, as digital transformation strategy becomes central to business strategy, it necessitates a redefinition of roles—from quality control inspectors to chief executive officers (CEOs)—and a reimagination of methods across the board.
The infusion of digital technologies into quality control processes is not merely an upgrade but a revolutionary shift. It empowers quality control professionals with advanced tools like statistical process control, artificial intelligence (AI), and data analytics, thereby amplifying their capability to ensure product quality and reliability. This paradigm shift demands an acute focus on enhancing organizational culture to champion digital aptitude and innovation. For quality specialists, engineers, and inspectors, digital transformation initiatives offer a novel repertoire of methods to elevate their work, from software testing in software development to meticulous scrutiny in food production lines.
Supply chain management, too, benefits significantly from integrating digital transformation efforts, enabling businesses to operate more seamlessly and meet customer demands with higher reliability. The strategic investment in digital technologies facilitates not only process improvement but also the development of new business models that are responsive to the dynamic market environment and customer experience expectations.
At the heart of this transformation is the necessity for a robust digital transformation governance framework, supported by government agencies and international organizations, to ensure public health and safety while fostering innovation. Business leaders, including the C-suite, are called to be the vanguard of this change, steering their enterprises toward digital quality prowess by investing in new technologies, comprehensive training programs, and a culture of continuous improvement.
As we look to the future, it is clear that digital transformation in quality control and assurance is fundamentally changing not just how businesses operate but how they conceive the very notions of quality and excellence. The commitment to fulfilling quality requirements through digital technology represents a strategic alignment of business processes, manufacturing processes, and organizational strategies with the emerging demands of the modern world. Quality control and assurance professionals stand at the forefront of this shift, equipped with digital tools and methodologies to ensure that, whether it's through software development, supply chains, or manufacturing lines, the final product not only meets but exceeds customer expectations. The path forward for most organizations will be characterized by continual adaptation, investment, and a steadfast commitment to innovation—hallmarks of a business strategy that appreciates the intrinsic link between digital transformation efforts and the overarching goal of quality management.
In the wake of these revelations and insights, we invite industry stakeholders, from manufacturing executors to policy framers, to join us in pioneering the next frontier of quality control and assurance. This is not merely an invitation but a mandate to usher in a landscape where digital empowerment and impeccable quality coalesce into the backbone of your enterprise. Engage with us as we chart the course towards a digitally transcendent paradigm, where excellence in product and service quality is not the goal but the starting point. To move forward, to innovate, and to redefine the standards of quality in your industry, begin your digital transformation journey today. Enlist in our comprehensive seminars, workshops, and collaborative forums designed to equip you with the tools, knowledge, and network necessary to turn digital quality control from aspiration to operational reality. Act now; the future awaits.